Pneumatic artificial muscles consist of two main parts, a rubber bladder, and a woven fabric. By applying pressurized air, the bladder is caused to change its volume and the fabric translates this change to a linear contraction, which approximates the behavior of human muscles. Hence the Regensburg Robotics Research Unit uses these muscles in its antagonistically actuated exoskeleton.
The exoskeleton is used to support an operator’s strength regarding lifting objects. Recent researches also examine the implementation of telerobotic scenarios, where the exoskeleton is used to remotely operate a robotic system and gives the operator a direct haptic feedback. To achieve a precise feedback a control architecture based on the entire exoskeleton is needed and as the main part, the relation between force, contraction, and pressure of the artificial muscles has to be determined.
To obtain the characteristics of these muscles, the Regensburg Robotics Research Unit has developed an automated process for muscle testing and recording of experimental data via a KUKA KR 240-2 robotic system with force and laser distance sensors, as well as a camera system for image processing. To collect the data, the muscles are stressed by the robot arm at various states of pressure and contraction. Derived from the measurements a characteristical diagram of force, pressure, and contraction is obtained.
In order to approximate the characteristics for model-based controlling purposes, the behavior is modeled with a mass-spring, as
well as a polynomial approach. By post-processing, the experimental data, the parameters of these models are estimated with a least squares method to fit the surface functions to the set of collected data points. The goal is to describe the relations between force, pressure and linear contraction in the most simplistic way in favor of simplifying the transfer function through model-based controlling.
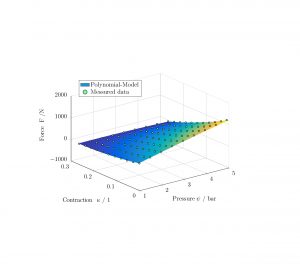
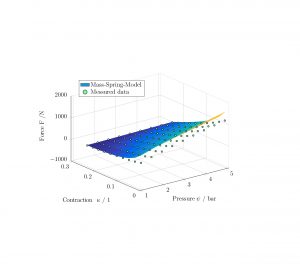